Kinetic Energy Recovery System for the Automotive Industry
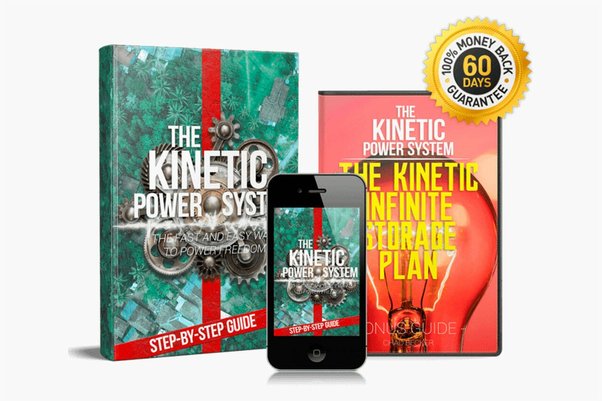
Click here to know more –
Formula 1 has a long-standing history of providing technological developments, which are applicable not only to fast racing cars but also to the general automotive industry. One such development is the Kinetic Energy Recovery System also called regenerative braking that has become a familiar subject in technical universities and automobile companies.
What is KERs?
The running of a Formula 1 car releases kinetic energy and the application of a brake converts it into a huge amount of heat energy that would be wasted normally. In a KERS equipped car, this is not the same. With the KERS system, when the driver applies the brake, this kinetic energy is converted into electrical energy.
Formula 1 cars have an electric motor and batteries set-up that is used for converting and storing the energy in the car. At one end of the engine crankshaft, the electric motor is mounted. The application of the brakes causes the electric motor to capture a portion of the rotational force and converts the kinetic energy into electrical energy, which is stored in the battery bank.
The pressing of the boost or KERS button by the driver causes the stored energy to be converted to kinetic energy giving the Formula 1 car additional horsepower for a limited duration.
Initially, this system was introduced in 2009 and very few F1 teams used this technology. KERS was banned in 2010, but was introduced again in 2011 and is being used presently by most of the F1 teams. The KERS system may be a bit heavy adding 35 kg offering a challenge for the F1 car balance, it does offer the driver approximately 80 bhp extra for up to 6.67 seconds per lap.
The release of this extra capacity may be done at one go or at different points providing the driver an additional advantage during overtaking or defending positions. The KERS system is not only intended to help in overtaking/defending to create additional excitement in the race, but is also a step towards bringing the sport close to “greenness”.
Testing KERS Systems
The high precision power analyzers of Yogokawa are used in the development of KERS in the F1 industry. Engineers can test several parameters in both R&D and production of the KERS system. Electric motor testing is a key application area for Yokogawa’s high precision WT1800 and WT3000 power analyzers.
Users are assisted in measuring electrical output, efficiency and losses in electric motors. The ability to connect 6 power inputs to a single WT1800 helps customers to evaluate motor input/output efficiency. Furthermore, the motor evaluation function simultaneously measures voltage, current and power as well as changes in rotation speed and torque derived from sensors. These sensors also enable the direction and shaft power to be measured.
The 6 inputs of the WT1800 also help customers to evaluate the battery charge and discharge characteristics, and the inverter’s efficiency. The Yokogawa WT3000 is the world’s most stable and accurate power analyzer providing the highest guaranteed accuracy of 0.02%.
Leave a Reply